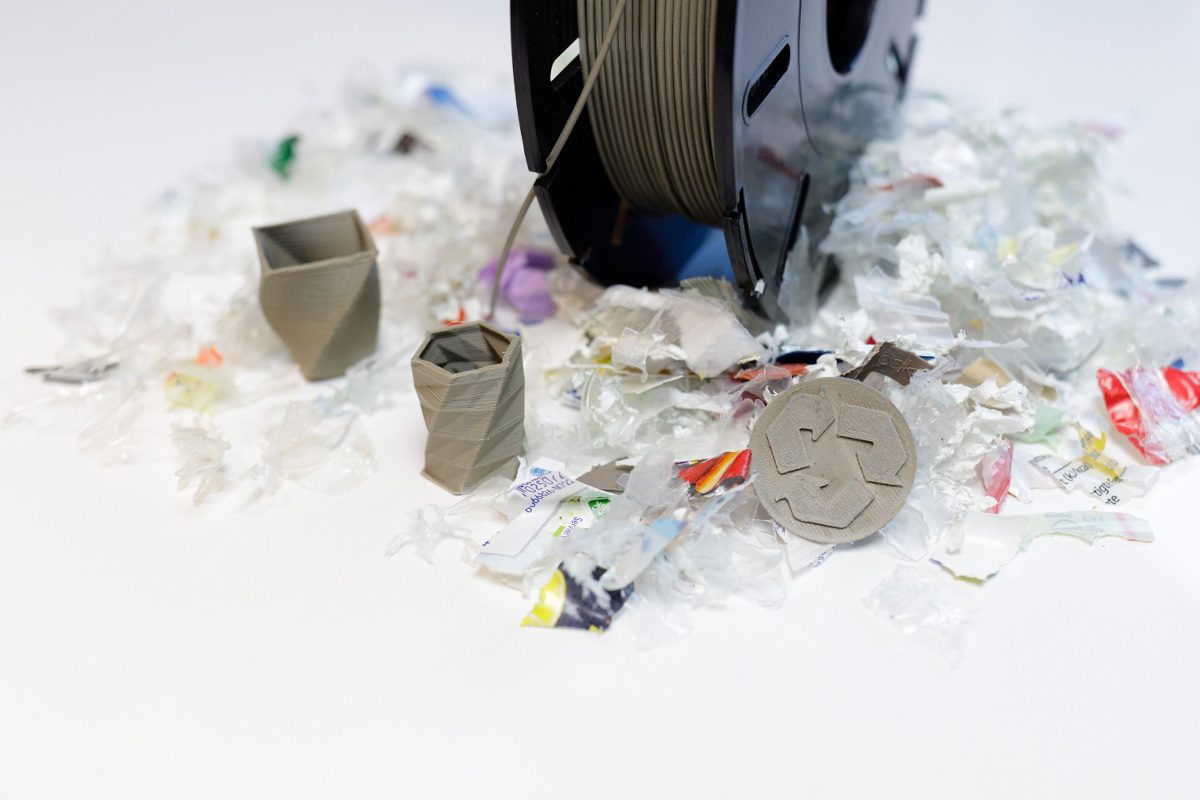
A brand new undertaking in Germany demonstrates an revolutionary methodology for turning plastic packaging waste into high-quality 3D-printed merchandise
Of the 5.6 million metric tons of plastic packaging that leads to family waste in Germany yearly, after getting used simply as soon as, lower than a 3rd of it may be recycled. The Fraunhofer Institute for Manufacturing Expertise and Superior Supplies IFAM has labored in partnership with Hochschule Bremen — Metropolis College of Utilized Sciences to attempt to do one thing extra attention-grabbing with this materials.
The portions of plastic waste being produced are steadily rising (presenting one thing of a conundrum as to what needs to be achieved about it). Packaging waste specifically is a significant contributor to this. The place German households produced 2.1 million metric tons of plastic waste in 1994, the determine had risen to five.6 million by 2023. That makes it much more essential to seek out methods to recycle these single-use merchandise, most of that are based mostly on crude oil.
“However it’s a lot tougher to recycle post-consumer waste than plastic residue left over from industrial manufacturing,” mentioned Dr Silke Eckardt, a professor specializing in sustainable power techniques and useful resource effectivity at Hochschule Bremen — Metropolis College of Utilized Sciences (HSB). In spite of everything, these supplies aren’t solely extremely heterogeneous however typically additionally soiled. To shut the manufacturing cycle however, HSB has teamed up with researchers at Fraunhofer IFAM to recycle even these tough-to-handle plastics from non-public households after which put them to make use of in additive manufacturing.
Recycled plastic utilized in filaments for 3D printing
“For the reason that waste is meant to be recycled to be used in 3D printing, it has to fulfill very stringent necessities for points comparable to purity, form and measurement,” mentioned Dr Dirk Godlinski, a undertaking supervisor within the Composite Expertise working group at Fraunhofer IFAM.
To this finish, the polypropylene output from a sorting plant for packaging waste was utilized in a feasibility research carried out by HSB and Fraunhofer IFAM.
To make sure adequate purity, Eckardt and her workforce processed the sorting plant output additional: On the college’s Laboratories for Round Economic system, they floor up the plastic, washed it and separated undesired materials from the principle stream utilizing a float-sink-separation. The workforce used near-infrared know-how to establish residual overseas plastics and eliminated them subsequently. After that, the researchers floor down the fabric once more till it had reached the grain measurement required for compounding and dried it. This methodology achieved purity ranges of greater than 99.8 p.c.
Then Fraunhofer IFAM took over: “Within the undertaking, we produced homogeneous polypropylene from the ready waste,” Godlinski mentioned. “This can be a versatile type of plastic that’s sturdy, immune to breaking and comparatively versatile.”
The analysis scientist and his workforce produced a strong plastic strand. First, they processed the flakes of recycled polypropylene in an industrial extruder at Fraunhofer IFAM. The fabric was mixed there, combined utilizing completely different extruder screw geometries, then melted at temperatures larger than 200 levels Celsius and extruded.
“The experience consists in exactly adjusting the assorted mechanical screws, temperatures, pressures and speeds alongside the manufacturing course of so the ultimate product is homogeneous polypropylene,” Godlinski defined. For additional processing in 3D printing, for instance, the strand have to be spherical and constant in diameter over its whole size, with a easy floor.
The researchers succeeded on this: The grey plastic strand, about two millimeters thick, was ready for use immediately as a filament in a industrial 3D printer. By now, Godlinski and his workforce have efficiently printed their first parts, together with caps.
This marks the conclusion of the feasibility research by HSB and Fraunhofer IFAM. The researchers are actually optimizing the manufacturing course of. Concepts for follow-up initiatives have already been floated. Godlinski notes that plastics might be additional refined, for instance, by introducing components comparable to glass fibers throughout compounding. This makes it potential to provide even very high-quality parts to be used in fields comparable to aviation and the automotive trade.
Authorized stipulations are additionally pushing elevated demand for recycled supplies: Beneath the EU Packaging and Packaging Waste Regulation (PPWR), packaging have to be composed of wherever from 10 to 35 p.c recycled supplies by 2030, relying on the kind of plastic and the product, excluding medical units and pharmaceutical merchandise. The requirement for 2035 is 25 to 65 p.c recycled supplies.