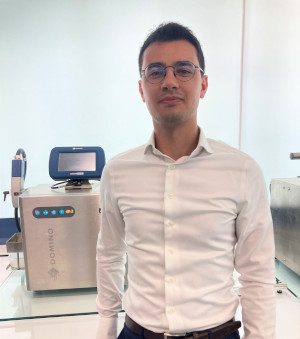
Thomas Guerriero outlines the interconnection between the environmental sustainability targets of manufacturing equipment producers and their manufacturing clients and examines the methods organisations can work collectively to have a net-positive contribution to minimising GHG emissions.
As the worldwide deal with environmental sustainability intensifies, the manufacturing business finds itself at a important juncture. Worldwide, the business is a major contributor to greenhouse fuel (GHG) emissions, accounting for roughly 1 / 4 of worldwide emissions.
On the firm stage, taking steps to cut back emissions is essential to assembly world local weather targets, making certain long-term competitiveness and sustainable growth, and staying compliant with present and future laws. But, the nuances are advanced and understanding the interaction between various kinds of emissions throughout the availability chain is important for driving significant and sustainable change.
Aligning sustainability commitments
The environmental efficiency of a manufacturing equipment producer will in the end additionally affect the environmental efficiency of their manufacturing clients (e.g. FMCG or model producers), and vice versa. As such, enhancements in environmental efficiency will necessitate collaboration up and down the availability chain to align commitments.
So, what steps can equipment producers take to assist align these commitments and create a extra environmentally sustainable future?
Creating extra sustainable equipment
Manufacturing equipment and tools have a direct influence on FMCG producers’ GHG emissions. There are a number of methods equipment producers can undertake and embed inside their design processes to create extra sustainable merchandise and assist their clients’ sustainability targets:
- Accountable materials sourcing: Be certain that equipment is designed to optimise the usage of recycled and recyclable supplies in product growth and packaging. With the upcoming EU Deforestation Regulation, equipment producers should guarantee they’re contributing to accountable sourcing, notably for packaging supplies like pulp and paper.
- Vitality effectivity: Establish alternatives to cut back vitality consumption throughout equipment operation. For instance, designing tools with trendy electrical drive programs rather than pneumatic programs, or which don’t require extra manufacturing unit air for cooling, can considerably decrease vitality use.
- Longevity in design: Develop strong equipment designed for sturdiness. The longer a product stays within the subject, the extra embedded emissions may be unfold over its operational lifespan, thus reducing total influence.
- Information-driven design: Equip manufacturing line equipment with good expertise to supply FMCG producers with insights on vitality consumption relative to manufacturing output. This knowledge can assist companies determine inefficiencies and supply perception (for each equipment producers, and their FMCG-manufacturing clients) on methods to optimise manufacturing operations for the longer term.
Decreasing waste within the manufacturing unit and past
Equipment producers may play a task in minimising waste generated at buyer FMCG manufacturing websites, from authentic equipment and consumables packaging to manufacturing line waste from product packaging supplies. The next methods can assist scale back waste manufacturing:
- Revolutionary packaging options: Collaborate with FMCG producers to develop equipment able to processing recyclable, compostable, or refillable supplies. This proactive method can assist FMCG producers to handle client demand for sustainability – 55% of customers prioritise environmental accountability in model alternative – and may assist the round economic system by serving to to cut back downstream waste.
- Environment friendly manufacturing processes: Design equipment that helps waste discount efforts throughout manufacturing. Late-stage customisation utilizing coding and marking tools can assist to cut back packaging waste from overstock, for instance. On the similar time, environment friendly materials utilization in product design may considerably scale back extra waste.
- Reliability, upkeep, and integration: By designing equipment to be dependable and simple to service and keep, equipment producers can assist their clients improve effectivity and uptime. Equally, built-in and automatic options can scale back the danger of waste resulting from handbook errors by limiting handbook steps concerned in knowledge entry and manufacturing line changeovers. In sectors like dairy, the place merchandise have a brief shelf life, stopping downtime and eliminating the danger of errors is important to lowering waste.
- Cloud communications and good programs: Designing manufacturing line equipment with in-built or related clever programs, comparable to sensors, machine imaginative and prescient programs, and cloud connectivity, can assist FMCG producers determine manufacturing points early – whether or not they is perhaps a calibration, ink, or unscheduled upkeep subject – stopping extra waste resulting from errors or malfunctions.
The way forward for manufacturing: Creating new sustainable enterprise fashions
Because the demand for sustainability grows, equipment producers should rethink conventional enterprise fashions to raised align with their FMCG-manufacturing buyer commitments. Listed below are some revolutionary approaches that equipment producers ought to discover to assist this aim:
- Assist for reuse and refurbishment: Develop schemes that facilitate the reuse and refurbishment of older equipment. This not solely extends the general tools lifecycle but additionally reduces the necessity for brand spanking new sources, minimising environmental influence.
- Recycling and refill initiatives: Work with FMCG producers – and the downstream provide chain – to design and implement programmes to assist the recycling and refill of consumable merchandise. By actively contributing to a round economic system, equipment producers can assist their clients scale back waste and emissions related to single-use objects.
- Design for longevity and modularity: Create tools designed for lengthy life and ease of service. Modular designs permit for upgrades and expansions as wanted, lowering the need for full replacements and conserving sources over time. Moreover, distant, superior monitoring companies can improve assist, serving to tools to perform extra effectively.
- End result-based manufacturing fashions: Shift from a product-focused mindset of promoting equipment to an outcome-based method targeted on options. In such fashions, equipment suppliers take accountability for making certain that tools operates at optimum capability, specializing in efficiency or outcomes versus transactional gross sales. This method can result in extra sustainable operations as producers and types optimise equipment utilization.
Conclusion: A collective path ahead
The manufacturing business is at a pivotal second in its journey towards environmental sustainability. Equipment producers can play a significant position in serving to scale back GHG emissions throughout the availability chain by aligning their sustainability commitments with these of their FMCG-manufacturing clients. Creating extra sustainable equipment, specializing in efforts that minimise waste, and innovating new enterprise fashions are important steps that we are able to take to foster a tradition of environmental accountability.
In the end, environmental sustainability in manufacturing isn’t just an operational problem however a possibility to innovate and lead in a quickly altering world. By working collaboratively with producers, manufacturers, and customers, equipment producers can create options that improve their very own sustainability profiles whereas contributing to a more healthy planet for future generations.