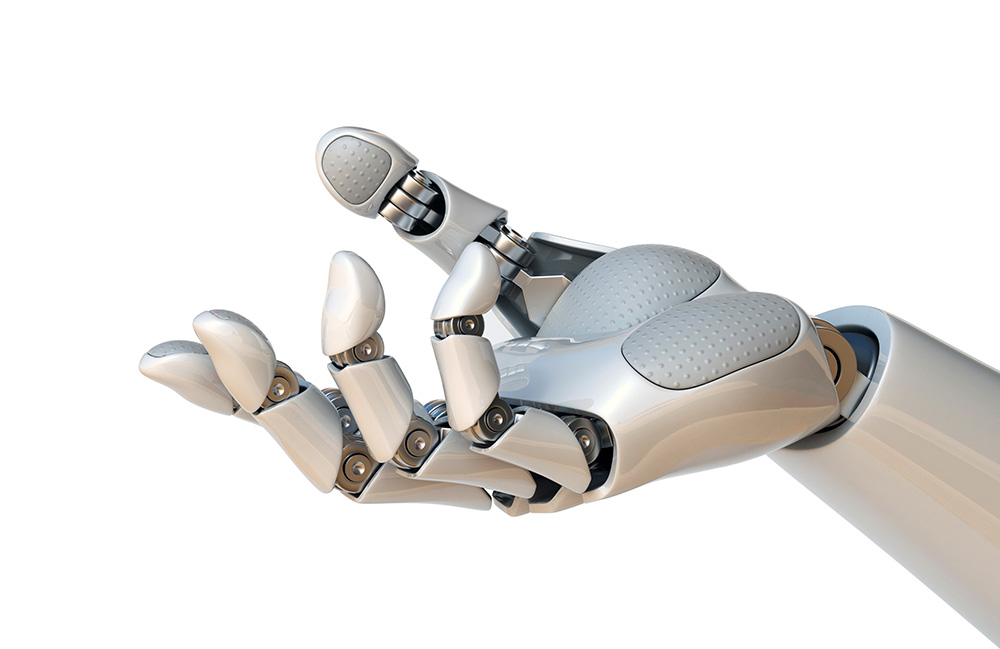
Humanoid robots depend on high-performance brushed DC motors to optimize their movement. | Supply: Adobe Inventory
Humanoid robots, a few of that are designed to function in shut interplay with people, rely closely on easy and managed joint and limb movement. This makes the number of the brushed DC motors that energy the axes of movement crucial.
Along with excessive torque density and responsiveness, effectivity to allow lengthy battery life is vital. Reliability is vital. Reaching freedom of motion requires integrating quite a few axes of movement, which is greatest completed by working intently with an professional on this area.
In schooling and remedy functions, humanoid robots are used to help hands-on studying and improvement throughout a variety of topics and necessities. Within the examine of engineering, college students can develop expertise in programming. Whereas in well being and remedy settings, sufferers can obtain rehabilitative care via human-robot interplay.
Humanoid robots could be geared up with a “mind” tailor-made to their particular duties, supported by focused programming and synthetic intelligence. Regardless of this customization, they share a typical human-like kind, together with palms or grippers.
Whereas sensors and instruments could be added for bodily modularity, the motor talent necessities for humanoid robots stay broadly comparable throughout varied duties.
Register in the present day to avoid wasting 40% on convention passes!
Humanoids should transfer in lots of instructions easily
For robotic builders, the overall universality in bodily movement permits a single humanoid design for use as a foundation for a number of functions. Nevertheless, to realize this scale of motion and utility for widespread duties, humanoid robots sometimes must optimize 20 or extra levels of freedom. Accordingly, the operational efficiency of the actuators that energy these axes of movement is essential.
Portescap, which designs and manufactures miniature motors, just lately specified a movement answer for an present humanoid robotic design. The robotic producer wanted compatibility with its present drives and controls however wished to extend torque density and scale back mass. This may be central to bettering the robotic’s precision by optimizing management of motion, growing responsiveness, and lowering inertia.
The robotic developer additionally wished to increase the battery lifetime, so the motors wanted to have excessive effectivity. With greater than 20 motors per unit and robots used throughout a various array of environments, reliability was additionally a precedence. The comparatively excessive variety of motors per robotic, mixed with the buying calls for of the end-user markets, meant that the necessity to stability value with worth was additionally vital.
The engineering workforce decided that the traits of a brushed DC motor would greatest fulfill the necessities. Offering simplicity of management, this motor design would guarantee integration with the humanoid’s present structure.
Whereas reaching the associated fee level required by the OEM, the inherent traits of a brushed DC motor can be well-matched to a humanoid’s shut human interplay, the place some great benefits of excessive torque at low pace would allow wonderful management.
All about brushed DC motors
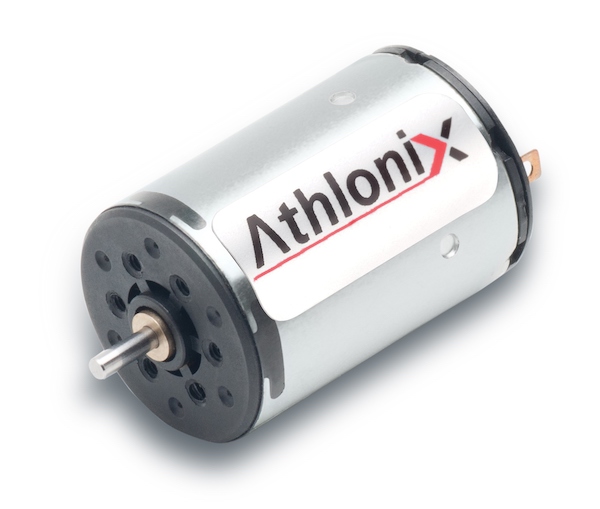
Coreless DC motors just like the Portescap Athlonix vary can enhance dynamism and effectivity. | Supply: Portescap
Why brushed DC motors? They provide quite a lot of options which might be helpful in robotic functions. Right here’s an summary of brushed DC motor design, and particularly some great benefits of coreless DC motors.
A typical brushed DC motor consists of an outer stator, sometimes made from both a everlasting magnet or electromagnetic windings, and an interior rotor made from iron laminations with coil windings. A segmented commutator and brushes management the sequence during which the rotor windings are energized, to supply steady rotation.
Coreless DC motors get rid of the laminated iron core within the rotor. As a substitute, the rotor windings are wound in a skewed, or honeycomb, vogue to kind a self-supporting hole cylinder or “basket.” As a result of there is no such thing as a iron core to help the windings, they’re usually held along with epoxy.
The stator is made from a rare-earth magnet, corresponding to neodymium, AlNiCo (aluminum-nickel-cobalt), or SmCo (samarium-cobalt). It sits contained in the coreless rotor.
The brushes utilized in coreless DC motors could be made from treasured metallic or graphite. Treasured metallic brushes (silver, gold, platinum, or palladium) are paired with treasured metallic commutators. This design has low contact resistance and is usually utilized in low-current functions.
When sintered metallic graphite brushes are used, the commutator is made from copper. The copper-graphite mixture is extra appropriate for functions requiring larger energy and better present.
The development of coreless DC motors offers a number of benefits over conventional, iron-core DC motors. First, the elimination of iron considerably reduces the mass and inertia of the rotor, so very fast acceleration and deceleration charges are potential.
As well as, no iron means no iron losses, giving coreless designs considerably larger efficiencies (as much as 90%) than conventional DC motors. The coreless design additionally reduces winding inductance, so sparking between the brushes and commutator is diminished, growing motor life and lowering electromagnetic interference (EMI).
Motor cogging, which is a matter in conventional DC motors as a result of magnetic interplay of the everlasting magnets and the iron laminations, can also be eradicated since there aren’t any laminations within the ironless design. And in flip, torque ripple is extraordinarily low, which offers easy motor rotation with minimal vibration and noise.
As a result of these motors are sometimes used for extremely dynamic actions (excessive acceleration and deceleration), the coils within the rotor should be capable to face up to excessive torque and dissipate important warmth generated by peak currents. As a result of there’s no iron core to behave as a warmth sink, the motor housing usually accommodates ports to facilitate pressured air cooling.
The compact design of coreless DC motors lends itself to functions that require a excessive power-to-size ratio, with motor sizes sometimes within the vary of 6 to 75 mm (0.2 to 2.9 in.), though sizes right down to 1 mm (0.03 in.) can be found, and energy scores of usually 250 W or much less.
Coreless designs are an particularly good answer for battery-powered units as a result of they draw extraordinarily low currents at no-load circumstances.
Coreless DC motors are used extensively in medical functions, together with prosthetics, small pumps (corresponding to insulin pumps), laboratory tools, and X-ray machines. Their capability to deal with quick, dynamic strikes additionally makes them appropriate for robotic functions.
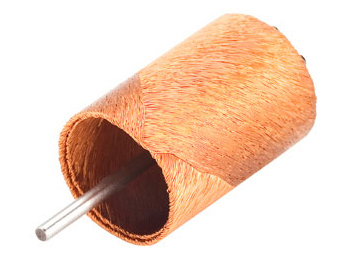
Coreless dc motors have a rotor that’s hole and self-supporting, which reduces mass and inertia. | Supply: Portescap
Coreless motor design can scale back mass
Portescap specified a 16DCT Athlonix motor, primarily based round a coreless design. This protects important weight in comparison with incorporating a standard iron core and permits larger responsivity and smoother movement, due to diminished inertia.
Neodymium magnets may also enhance torque density by reaching a stronger magnetic area, enhancing the interplay with the motor windings.
The coreless design was additionally specified to extend effectivity and scale back vitality consumption by eradicating the results of hysteresis and eddy present losses related to a traditional iron core DC motor. Treasured metallic commutation can improve effectivity by lowering resistance and minimizing the voltage drop throughout the brush-commutator interface.
The optimized ironless building of the motors allowed cooler operation and improved energy density. Motor inductances have been adjusted to match drive necessities, making certain optimum pace and torque traits.
To additional reduce weight, the engineers custom-made the windings with light-weight, self-supporting coils. Mixed with the coreless design and neodymium magnets, these benefits achieved as much as an 8% discount in motor diameter whereas delivering the required torque.
To additional enhance sturdiness, in addition to enhance torque switch, the engineers additionally built-in the pinion gear into the motor shaft. This method would optimize alignment and improve management at every axis, minimizing play, which might additionally scale back mechanical put on.
Because of the collaboration between the robotic and movement engineering groups, the developer was capable of obtain the focused measurement and weight in addition to the required movement profile for every axis.
Editor’s notice: This text was syndicated from The Robotic Report sibling website Movement Management Ideas.